AMS 5662 Certified Inconel 625 Bar with Corrosion and Heat Resistance
Description:
Inconel 625 is a corrosion and oxidation resistant nickel alloy that is used both for its high strength and outstanding aqueous corrosion resistance. Its outstanding strength and toughness is due to the addition of niobium which acts with the molybdenum to stiffen the alloy’s matrix. Alloy 625 has excellent fatigue strength and stress-corrosion cracking resistance to chloride ions. This nickel alloy has excellent weldability and is frequently used to weld AL-6XN. This alloy resists a wide range of severely corrosive environments and is especially resistant to pitting and crevice corrosion. Some typical applications Inconel 625 is used in are chemical processing, aerospace and marine engineering, pollution-control equipment, and nuclear reactors.
Limiting Chemical Composition (%):
Nickel: 58.0 min |
Chromium: 20.0-23.0 |
Iron: 5.0 max |
Molybdenum: 8.0-10.0 |
Niobium (plus Tantalum): 3.15-4.15 |
Carbon: 0.10 max |
Manganese: 0.50 max |
Silicon: 0.50 max |
Phosphorus: 0.015 max |
Sulfur: 0.015 max |
Aluminum: 0.40 max |
Titanium: 0.40 max |
Cobalt: 1.0 max |
|
Applications:
1,Chemical processing equipment
2,Oil & Gas sour service flowlines
3,Well head equipment
4,Chemical injection lines for Oil & Gas wells
5,Heat exchangers
6,Aerospace and marine engineering,
7,Pollution-control equipment
8,Nuclear reactors.
Features:
1,High creep-rupture strength
2,Oxidation resistant to 1800°F
3,Seawater pitting and crevice corrosion resistant
4,Immune to chloride ion stress corrosion cracking
5,Non-magnetic
.

Forms Available:
Rod, bar and forging, etc.
Standards:
Rod, Bar, Wire and Forging Stock
ASTM B 446/ASME SB 446 (Rod & Bar),
ASTM B 564/ASME SB 564 (Forgings),
SAE/AMS 5666 (Bar, Forgings, & Rings).
Packing and Shipping
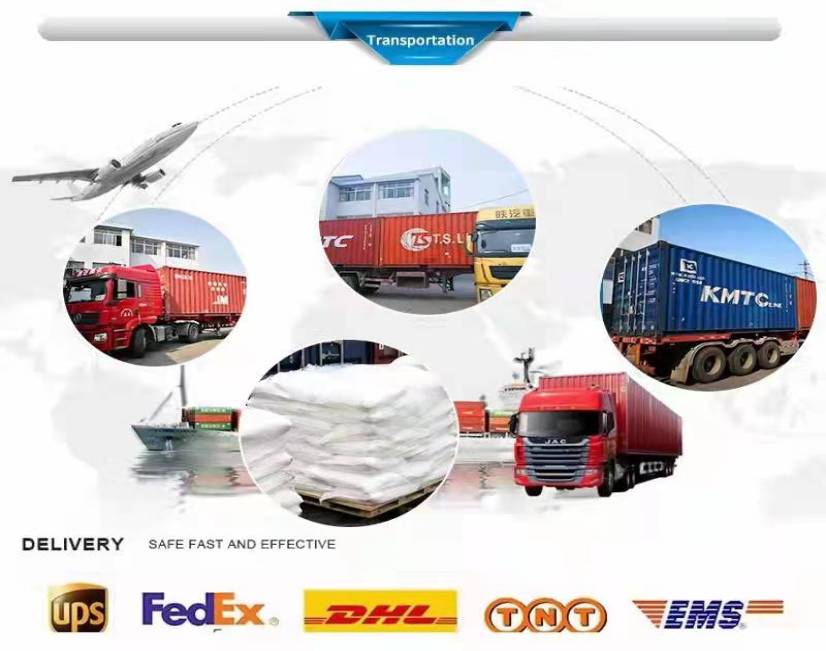
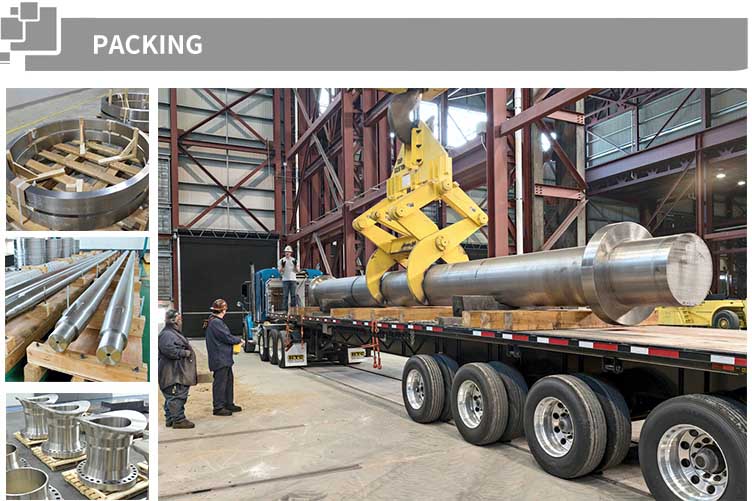