Factory Direct Pricing Super Alloy Waspaloy Round and Flat Bar GH4738
Description:
GH4738 (UNS N07001, W. Nr. 2.4654) is a Ni-Cr-Co based precipitation hardening deformation superalloy with a service temperature below 815℃. Cobalt, chromium and molybdenum elements were added to the alloy for solution strengthening, aluminum and titanium elements were added to form ‘γ’ precipitation strengthening items, boron and zirconium elements were added to purify and strengthen grain boundaries. The alloy has high yield strength and fatigue resistance at 760℃ to 870℃. It has good oxidation and corrosion resistance in gas turbine atmosphere below 870℃, excellent plasticity and stable microstructure. It is suitable for making turbine disc, industrial blade, high temperature fastener, flame tube, shaft and turbine casing etc. The main products are cold-rolled and hot-rolled plates, pipes, strips, wires and forgings, castings, bolts and fasteners, etc.
Limiting Chemical Composition (%):
Content | C | Cr | Ni | Co | B | Mn | P | Cu | As | Sb | SE |
Min | 0.03 | 18.0 | Bal | 12 | 0.003 | ||||||
Max | 0.10 | 21.0 | 15 | 0..10 | 0.10 | 0.015 | 0.100 | 0.0025 | 0.0025 | 0.0003 | |
Content | Mo | Al | Ti | Fe | Zr | Si | S | Pb | Sn | Bi | |
Min | 3.5 | 1.2 | 2.75 | 0.020 | 0.015 | ||||||
Max | 5 | 1.6 | 3.25 | 2,0 | 0.080 | 0.15 | 0.0005 | 0.012 | 0.00003 |
Applications:
Used for making turbine discs, blades and sealing rings for aeroengines, as well as smoke turbine blades, turbine discs and large bolts. The alloy is widely used in aviation, aerospace, petroleum, chemical industry and power generation equipment in the field of rotating parts, such as compressor blade, turbine disc, valve body, ring and shaft rotating parts.
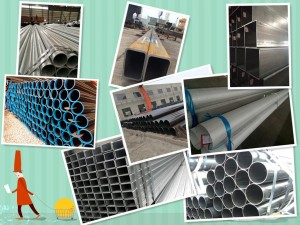
Features:
GH4738 has good oxidation resistance and corrosion resistance in various atmospheres for jet engine or similar working conditions. The oxidation resistance temperature can reach 1040℃ for continuous operation and 870℃ for intermittent operation. The alloy also has good corrosion resistance to salt-spray. Especially the solution treatment is the best. After the bar was treated at 1080℃×4h/AC+ stabilization + aging, the notch endurance tests at 650℃, 750℃ and 815℃ showed that the alloy had no notch sensitivity. After long-term aging at 650℃ and 730℃ to 3000h, no new phase precipitates and the microstructure is stable.
Forms Available:
Round and Flat Bar.